The ecological footprint of waterproofing based on material selection and labor costs
Properties and installation methods of waterproofing materials
Roll materials vs. white tank
In Europe, many materials are sold for waterproofing underground, reinforced concrete structures. But how aware are we of the properties of these materials, the methods of installation, and most importantly - what ecological footprint does the installation itself leave, as well as the various aspects after installation?
In the following, we will answer these questions and find out which material or solution is the greenest and most practical to use, keeping in mind the following:
- material consumption
- labor cost
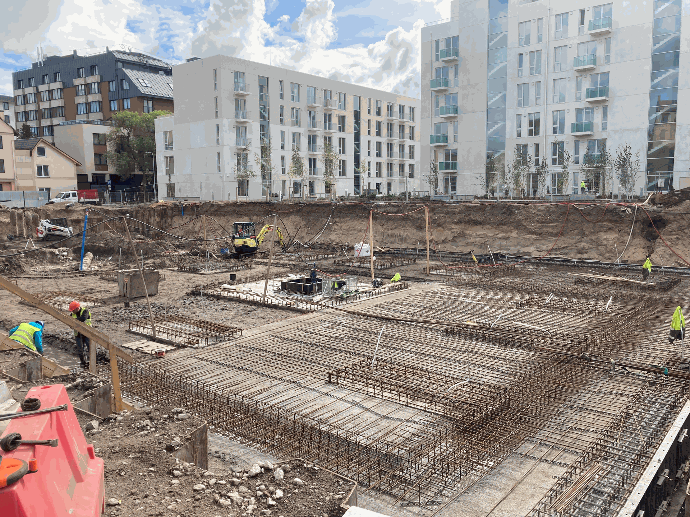
In the following article, we will look at what materials are used today to waterproof below-grade reinforced concrete structures and calculate their cost per m2. This helps us see the differences in the necessary quantities of materials, from which we can conclude financial savings and the reduction of the environmental footprint and labor costs.
We discuss the topic through materials used in practice. We bring out SBS, Köster KSK, and WFP Pre-Tec among the roll materials. We use a white tank, i.e., an integral waterproofing solution, for comparison.
BASE SURFACE
A good installation starts with a well-prepared substrate, which applies to all waterproofing membranes. The ideal surface is flat, clean, dry, and without holes. In addition, there must be no sharp protruding ends/cables, significant gaps, or cracks. In the case of a waterproofing membrane, it is essential to consider that the base surface must be exactly where the primer can be added, and when installing, the roll material can be glued to the structure.
In the case of a white tank, i.e., integral waterproofing, the smoothness of the substrate is not so important because no membrane is installed there. However, the quality of concrete and concrete works is important!
INSTALLATION PLACES
Waterproofing membranes can be installed both horizontally and vertically. The membrane waterproofs foundation slabs, wet rooms, basement floors, ceilings, balconies, and terraces.
The integral waterproofing solution is used in constructing cooling towers of power plants, reservoirs of water treatment plants and water treatment plants, tunnels and subways, concrete pipes, underground garages, parking garages, foundations, basements, bridges, viaducts, precast concrete elements, etc.
MATERIAL COMPARISON
SBS bitumen waterproofing membrane consists of bitumen (obtained from oil processing), modifier, and filler, and inside the materials is a support fabric or support layer. The higher the weight of the backing fabric (standard 140-200 g/m2), the stronger the SBS roll material. Generally, the thickness of the material is in the range of 2-5 mm, and when installing, the overlap between the two materials must be 5-10 cm, while the weight of one layer is in the range of 3.5-5 kg/m². The anti-stick film of the SBS roll material must be removed during installation. The easiest way to do this is by melting the film.
The substrate must be prepared as described above. For installation, the rolled material must be heat-welded using a gas torch until the bitumen melts, then gradually rolling the fabric onto the base surface. Hot bitumen must not come into contact with water, as this will result in sudden expansion and spontaneous triggering of the boiling process. In addition, steam from hot bitumen can slightly irritate the upper respiratory tract and eyes.
Burns can occur if hot liquid bitumen gets into the eyes or comes into contact with the skin. Solid bitumen does not cause skin irritation, but vapor from condensed bitumen can.
Safety glasses and special gasoline-proof gloves must be worn during installation. The material must be installed in at least two layers. After application, a detailed inspection must be carried out to ensure a good installation. SBS layers must be installed without air bubbles, folds, or other defects. SBS roll material provides waterproofing only when installed without defects and should not be installed in an explosive or narrow location.
Most product pages give SBS material a service life of about 20-25 years, meaning that the material must be renewed at least once to maintain the continuous waterproofing of a 50-year-old building.
Köster KSK is a self-adhesive waterproofing membrane consisting of a mixture of rubber bitumen with an HDPE cover film. Rubber, a membrane component, is a highly elastic natural or synthetic high-molecular substance. For example, waterproof natural rubber comes from South America and is used in making waterproof outerwear or shoes. HDPE cover film is high-density polyethylene.
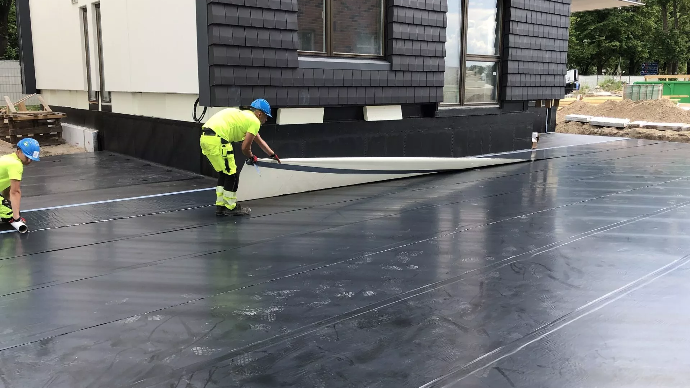
The film is characterized by excellent hardness, abrasion resistance, chemical resistance, and surface gloss. Since HDPE is more substantial than other types of polyethylene, it is also used, for example, in manufacturing canisters or pressing gas and water pipes. The total thickness of the membrane is 1.5 mm, and the overlap must be at least 50 mm. The weight is approximately 1.66 kg/m2.
Köster KSK is radon, methane, and water vapor tight based on tests performed by the manufacturer. Since the material is self-adhesive, it is unnecessary to heat treat the product or use additional equipment during installation.
WFP Pre-Tec is a pre-installed, especially laminated waterproofing membrane. The membrane consists of a plastic layer, an adhesive layer, and a granular bulk layer. The material is fully adherent to fresh concrete. In addition, a self-adhesive strip on one edge of the membrane helps create a watertight connection. The membrane is also radon and water-vapor-resistant. The thickness of the material is 1.5 mm, the weight is about 1.55 kg/m2, the mandatory overlay is 75 mm, and only ONE layer of material is required to achieve a watertight structure.
No additional equipment is required for installation, as the membrane is pre-installed and self-adhesive. The membrane is installed on a suitable load-bearing surface before the reinforcement and concrete works, and when concrete is cast, it self-adheres to the fresh concrete. However, it is essential to point out that the concrete must be cast at least 45 days after the installation of Pre-Tec and that the membrane can't be damaged during the concrete pouring.
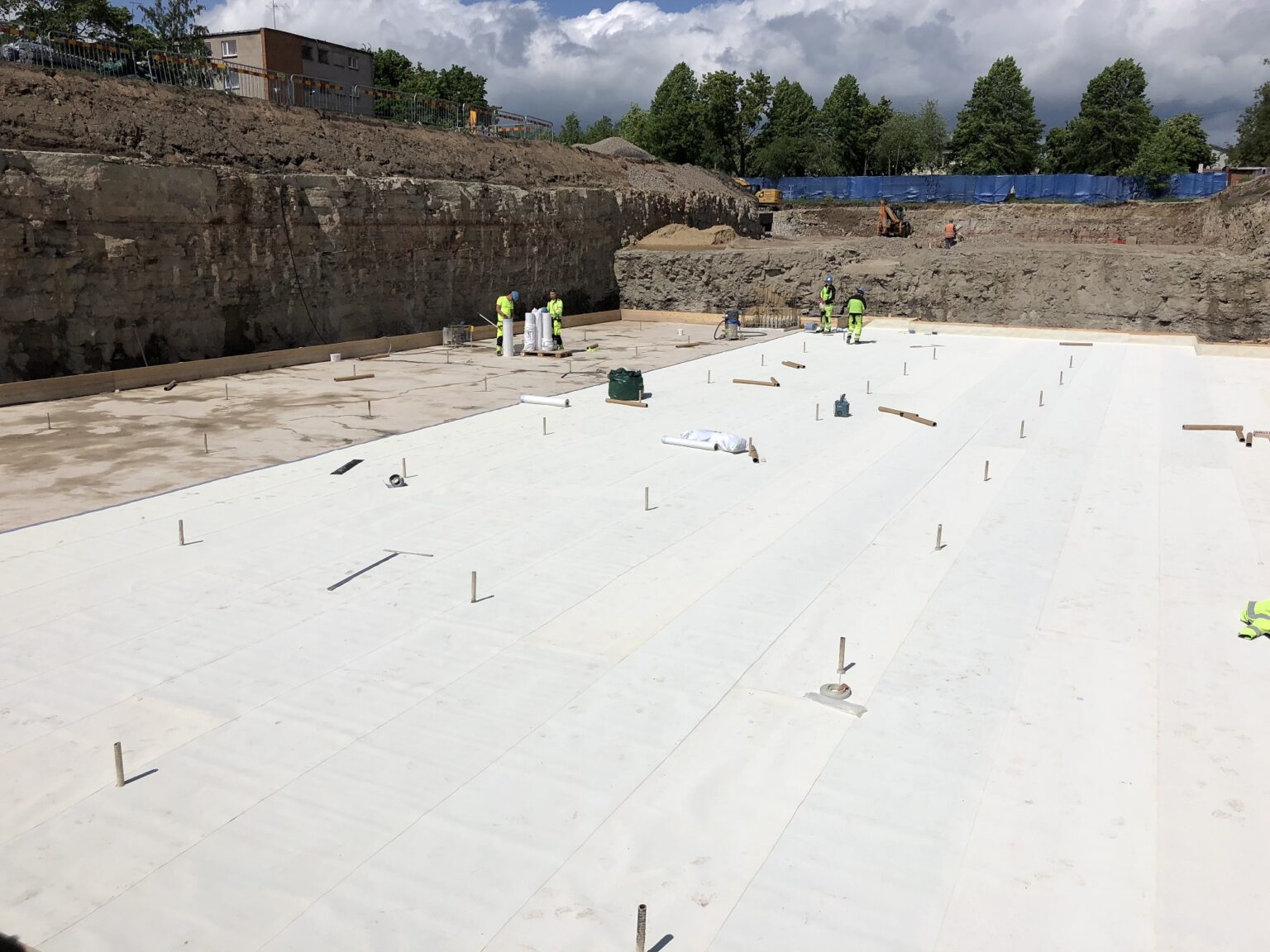
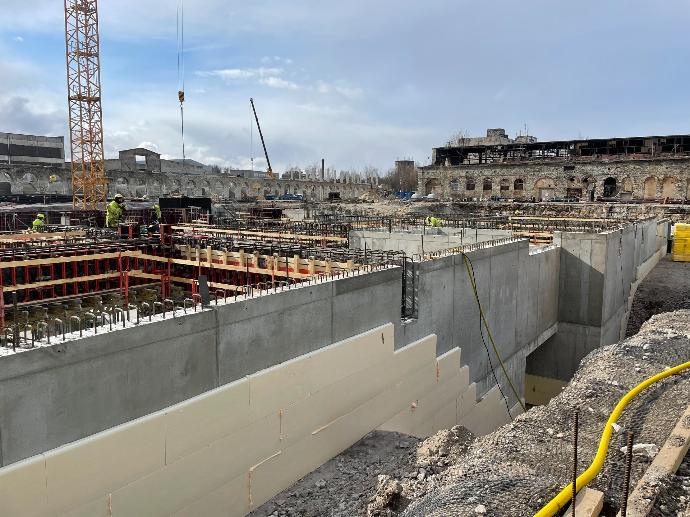
The white tank is the latest integral waterproofing solution with three primary materials. The first part consists of metal-sheet waterstops added to concrete construction joints before or during casting. The second part consists of the crack-inducing profiles that control and waterproof the shrinkage cracks, enabling larger concrete volumes to be cast. The third part is the crystalline waterproofing admixture added to the concrete mix at the concrete factory. The latter gives the concrete self-healing ability.
Concrete structures construction joints
Metal-sheet waterstops are installed to construction joints to prevent water ingress through the joints within the water pressure range specified on the product datasheet.
The metal-sheet waterstops are either 0.5 or 0.7 mm thick galvanized steel sheets. One side of the steel sheet is covered with a special mineral coating, which helps to ensure adhesion with concrete and better waterproofing of the construction joint.
The material consumption per m2 of WPM® metal-sheet waterstops 125R is 0.57kg/m, and WPM® 80R – is 0.32kg/m.
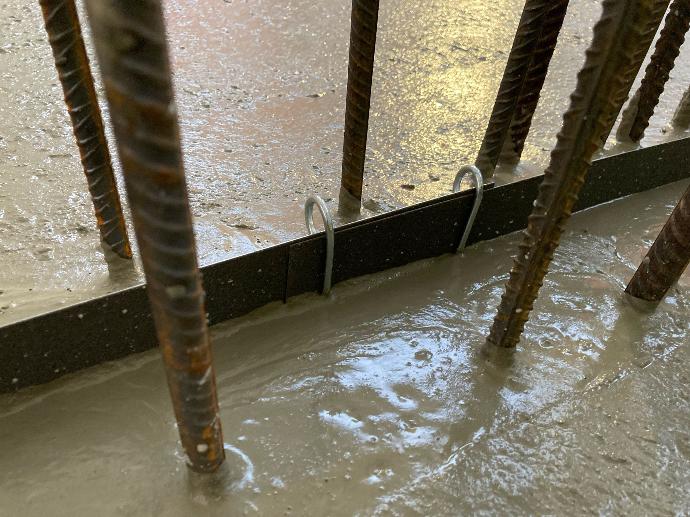
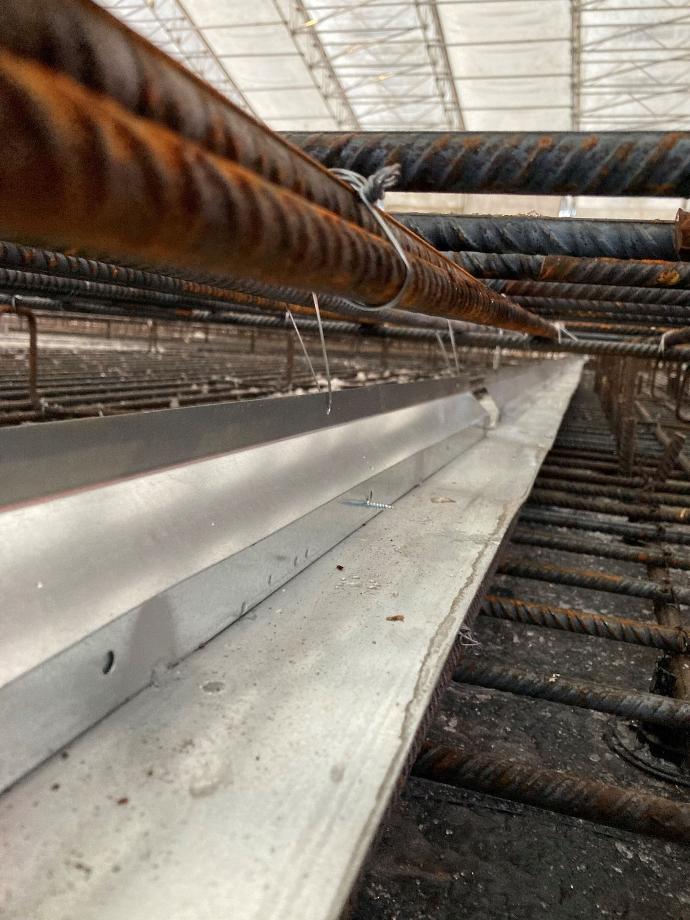
WPM®
Crack Inducing Waterstop profile
A Crack Inducing Waterstop is a metal sheet waterproofing element that controls and waterproofs shrinkage cracks in concrete structures. The planned shrinkage crack is immediately waterproof and located in the intended location. The profile has been tested to provide water tightness up to 4.5 bar water pressure.
The Crack Inducing Waterstop consists of a galvanized metal sheet covered on one side with a special elastic mineral coating. Z-shaped steel plates are connected perpendicularly to the galvanized mineral-coated steel sheet, which provides a binding keyway-shaped shrinkage crack, helping to maintain the strength properties of the structure. Although the width of the waterstop sheet is 150 mm, the Z-shaped steel sheet's height depends on the structure's thickness. The material consumption of WPM® Crack Inducing Waterstop (20/60/20) is 1.11+0.4= 1.51kg/m.
The crack-inducing element is installed between the rebars in the middle of the structure with a calculated distance from each other depending on the dimensions of the design.
Crystalline waterproofing admixture
The crystalline waterproofing admixture gives the concrete the ability to self-heal. With the water entering the crack, the admixture can close the static cracks in the concrete, with an opening width of less than 0.4 mm.
It is impossible to describe the reaction equations of the crystal structure formation process in more detail because the recipes and chemical composition of all additives that reduce the capillary water absorption of concrete are proprietary formulas of the manufacturers and are not public information.
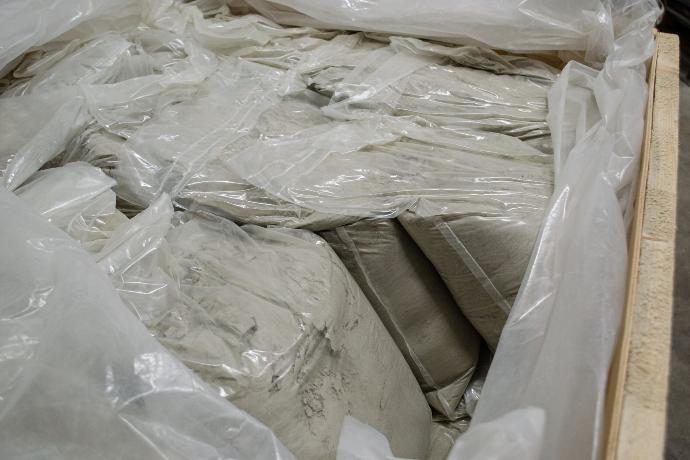
The additive does not act as a vapor barrier, promotes corrosion resistance, and does not damage rebars. Crystalline waterproofing admixture increases the compressive strength of concrete and protects concrete from carbonization and corrosion caused by chlorides and sulfates. The tested compressive strength of our product is 12 bar. The average consumption of the crystalline waterproofing admixture of WFP is 1m³= 3kg.
Before using an admixture, it is always important to perform compatibility tests and clarify the appropriate dosage and concrete quantities. When mixing, avoid lumps.
MATERIAL STORAGE
Newer waterproofing membranes can be stored for up to 24 months, and SBS materials can be stored for up to 12 months. The white tank waterproofing metals-sheet waterstops and profiles are preserved for 36 months, and the crystalline waterproofing admixture for 12 months. It should be noted that all products must be stored in cool, dry, and original packaging.
SUMMARY
All information presented in the article is based on product pages or public information. When comparing this data, it is clear that the weight of the materials is very decisive for the environment. Based on the calculations, you can determine how much waterproofing material is needed per m2 to ensure proper waterproofing that meets international standards.
Material cost
Next, we will look at calculations showing the material cost per m2 for all three types of waterproofing.
- The thickness of the SBS roll material is between 2-5 mm, and the overlay must be 50-100 mm - the weight is between 3.5 and 5 kg/m².
- In the case of Köster KSK, the numbers are almost two times smaller - the thickness of the membrane is 1.5 mm, and the overlay must be at least 50 mm. The weight remains at 1.66 kg/m2.
- For Pre-Tec, the readings are almost similar to Köster - the thickness of the material is 1.5 mm, and the overlay must be 75 mm. Only ONE layer of Köster KSK and WFP Pre-Tec material needs to be added. The weight is about 1.55 kg/m2.
To achieve waterproofing standards, at least two layers of SBS roll material must be installed, but one layer is sufficient for Köster KSK and WFP Pre-Tec. From this, we can conclude that compared to SBS, the material costs of Köster and Pre-Tec are almost four times lower. In addition, according to the product pages, the life of SBS is 25 years on average, while the life of Köster KSK and Pre-Tec is 50 years, which means that in the case of SBS, the material cost doubles even more in this context, resulting in a total of 8 times the cost.
Let's take a sample project to illustrate the material costs - a structure with a waterproofing area of 368m², of which the walls are 168m² and the floor 200m².
- For this project, the consumption of SBS roll material with metal-sheet waterstop is 9.7kg/1m², a total of 3776.9 kg waterproofing materials.
- In the case of classical waterproofing with metal-sheet waterstop, the material consumption is 2.1kg/1m², and the total material consumption of the sample project is 808.8 kg.
- We get 1.05kg/1m² for the material consumption for the white tank, i.e., internal waterproofing, which makes a total of 384.8 kg.
Labor costs
When calculating the labor cost based on the sample project, we consider that there are three people at work at the same time, and the length of their working days is 8 hours. Furthermore, the comparison is based on the minimum installation capacity during one working day (50m2). As a result, it takes 6-8 days for modern roll materials to completely waterproof the structure. In the case of SBS roll material, this number must be doubled because the material has to be installed in at least two layers, which means it takes 14-16 days. For a white tank, the labor cost for installing metal sheets and crack inducer profiles is about 1-2 days.
Conclusion
From the calculations, we can conclude that regarding material and labor costs, the white tank, i.e., an integral waterproofing solution is the most optimal and, thus, the greenest choice. With this in mind, structure design and the intended use must always be considered. In addition, it is also important to consider the structure's location and what conditions it must meet.
The integral waterproofing solution is more accessible and more convenient because all materials are installed into the structure while rebars are put into place, and the crystalline waterproofing admixture is added to the concrete in the concrete plant. So there is no need to do significant additional work to ensure waterproofing as for the membrane waterproofing.